Weighing and mixing system is a comprehensive automation system that integrates computer production process control and data management such as unloading, weighing, batching, formula control and discharging. It is suitable for industries that require a production process in which multiple materials are mixed in proportion. The entire weighing and compounding system is usually composed of the following subsystems: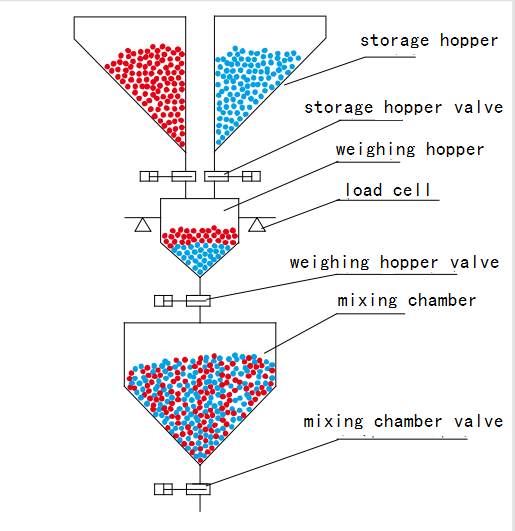 1. Unloading system; 2. Conveying system; 3. Metering and batching system; 4. Mixing unit; 5. Material storage system; 6. Dust removal system; 7. Central control system; 8. Auxiliary equipment.
The following introduces the composition and principle of each subsystem
1. Unloading system
The unloading system completes the process of entering the silo from bulk, barreled, bagged, and containerized raw materials.
Bulk materials can be sent directly to the storage bin through the pneumatic conveying device on the tank truck
The barreled material can be discharged by a hydraulic bucket reversing machine
The bagged materials are discharged by the bag-inverting station. The bag turning station is divided into a small bag turning station, a ton bag turning station and a common bag turning station. Among them, the pouch inverting station is divided into manual, semi-automatic and fully automatic. Tonnage pour bag station can also be divided into manual and fully automatic.
Container loading materials can be discharged through the container discharge system.
2. Conveying system
The transportation of materials is the key to the automation of the compounding production line. In the automatic compounding system, the conveying system occupies a large proportion. Including the transportation of raw materials from the unloading equipment to the weighing silo; the transportation of finished materials from the mixer to the finished silo; the transportation of finished materials from the finished silo to the extruder or other processing equipment;
The conveying system mainly has the following forms:
Screw conveyor (including flexible screw conveyor)
Vibration conveyor
Pipe chain conveyor
Pneumatic conveying (including vacuum feeder)
Bucket lifting is the same (including Z type bucket elevator)
3. Weighing and batching unit
In a fully automatic compounding system, the weighing and compounding system normally consists of two independent subsystems:
A set of main material weighing and batching system; the main material scale has a large rating and is suitable for main materials with high weighing ratio.
A set of auxiliary material weighing and batching system; the rated value of the auxiliary material scale is relatively small, suitable for materials with a small proportion.
This design helps to improve the accuracy of the batching. Each batching system is composed of various material hoppers, conveyor systems, batching weighing hoppers, etc.
Four, mixing equipment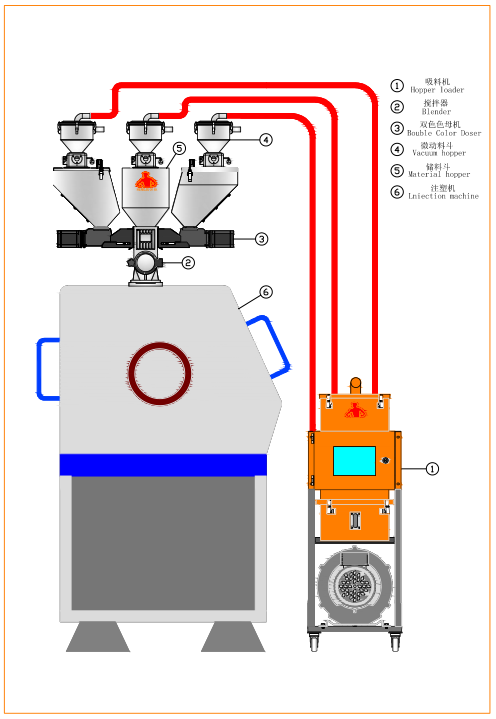 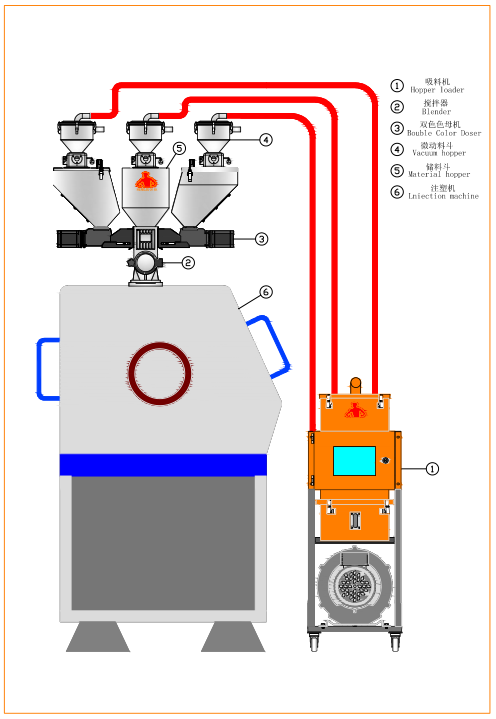 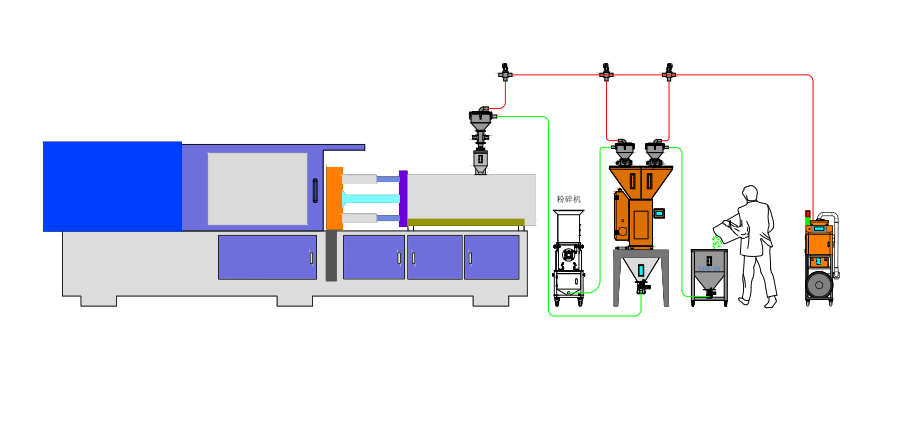
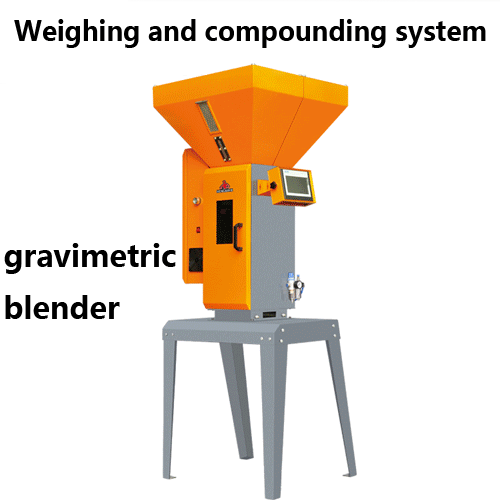
The mixing equipment can be divided into a continuous mixer and a gap mixer, and the appropriate mixing equipment can be selected according to the user's needs.
5. Material storage equipment
Material storage equipment mainly refers to various silos used for storage of raw materials and finished materials.
6. Dust removal system
According to the different occasions, the dust removal system will be designed according to the scene.
central control system
The control system can be adopted to control the touch screen system and the central control system according to the scale of the scene. The control system connects the whole set of equipment together, which is the guarantee for the long-term stable operation of the whole system. The control system can include on-site operation cabinet and central control system. It can realize the following functions.
Automatic detection function:
● Automatically detect the operation of all motors in the production process,
● Automatically detect various types of switches during the production process.
● Automatically detect the weight information of each batching scale and each formula in the production process,
|